Ultraschall Tauchtankprüfung
Der zeitabhängige Verlauf des Signals (A-Scan, A-Bild = zeitlicher Amplitudenverlauf) liefert die Echolaufzeit des Ultraschallpulses, also den Quotienten aus Laufstrecke und Geschwindigkeit des Ultraschalls (Bild1). Zwischen Sender und Prüfobjekt wird ein Koppelmedium (z.B. Glycerin, Wasser) benötigt. Die automatisierte Ultraschallprüfung findet daher in einem Tauchtank statt (Tauchtankprüfung, Bild 3 und 4). Möglich ist auch die Ankopplung über einen Wasserstrahl (Squittertechnik) oder einen Wasserfilm (Wasserspaltankopplung). Nach dem Durchlaufen der sog. „Wasservorlaufstrecke“ wird ein Teil der Welle an der Grenzfläche Wasser/Probe reflektiert und läuft zum Prüfkopf zurück („Eintrittsecho“). Ist der Werkstoff homogen, so erfolgt die nächste Reflexion erst an der Probenrückseite („Rückwandecho“). Sind jedoch innere Grenzflächen vorhanden (z.B. Korngrenzen, Poren, Fasern, Delaminationen oder Einschlüssen), so wird ein Teil der Welle schon vorher zurückgestreut („Fehlerecho“). Das Fehlerecho ist eine verfrühte Reflexion am geschädigten Bereich, dahinter entsteht ein Ultraschallschatten, der sich im Verlauf des Rückwandechos zeigt.
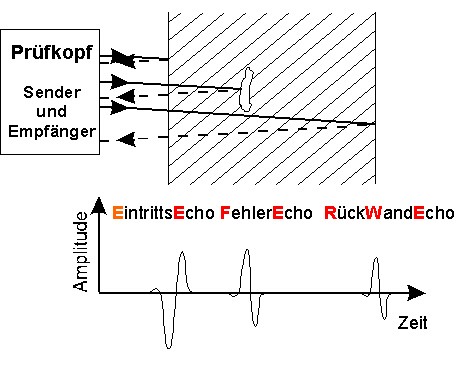
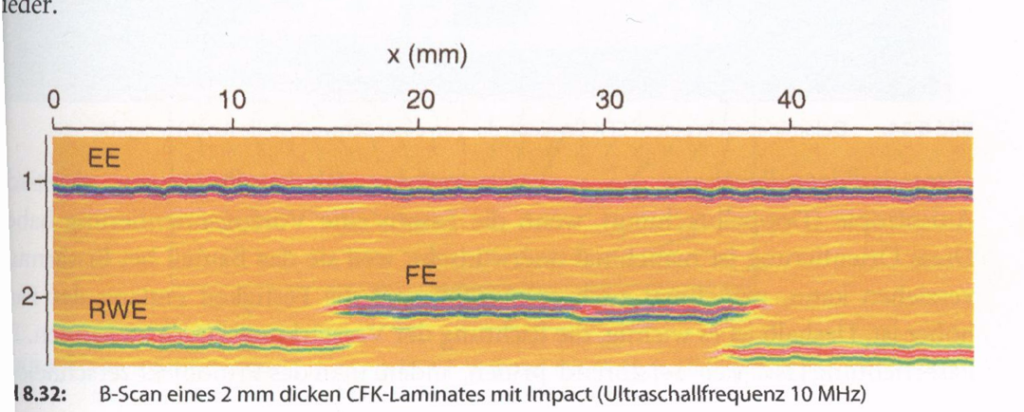
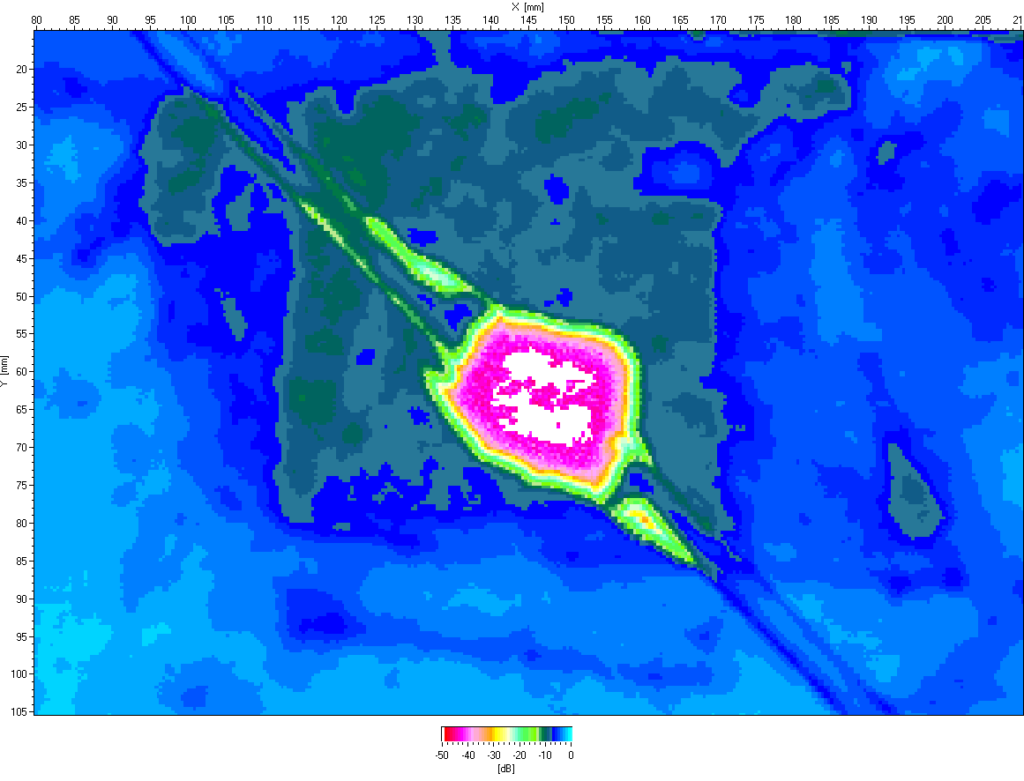
Ein B-Scan entsteht durch das Abfahren („Scannen“) einer Linie und der Digitalisierung der empfangenen A-Wellen. Die zweidimensionale Darstellung wird durch eine Grau- oder Farbwertdarstellung der Echoamplituden längs der Zeitachse gewonnen (Bild 2). Mit einem C-Bild wird ein zweidimensionales Schnittbild parallel zur Oberfläche erzeugt, bei dem die Amplitude der Ultraschallwelle entweder im potentiellen Fehlerbereich oder vom Rückwandecho ausgewertet wird.
Eine weitere Möglichkeit besteht in der Auswertung der Reflektion der Ultraschallwelle von einem Hilfsreflektor, der sich geeigneter Weise ca. 5 mm unterhalb der Rückseite des Bauteils befindet (Bild 6). Wird in dieser Darstellung statt der Amplitude die Laufzeit, bzw. die Tiefe der Anzeige ausgewertet, so spricht man von einem D-Scan. Bei modernen Ultraschallprüfanlagen können auch frequenzbasierte Merkmale evaluiert werden. Man spricht dann von einem Feature-Scan (F-Scan).
Neben diesen direkt bilderzeugenden Scanarten bieten Ultraschallprüfanlagen mit hohen Datenübertragungsraten die Möglichkeit, die A-Bilder in einem gewissen Laufzeitbereich zu digitalisieren und abzuspeichern. Dieser Vorgehensweise, Multi-C-Scan oder Vollwellenerfassung genannt, lässt eine nachträgliche situative C-Scangenerierung zu, wie sie im Laborbereich oftmals gefragt ist.
Ultraschall-Tauchtechnikprüfköpfe (Bild 8) gibt es in fokussierten und unfokussierten Ausführungen mit Mittenfrequenzen zwischen 0,5 und 100 MHz. Im Allgemeinen wird mit Prüffrequenzen zwischen 5 und 10 MHz gearbeitet. Bei Schallgeschwindigkeiten in Kunststoffen und Verbundwerkstoffen zwischen 2.000 und 3.000 m/s ergeben sich Wellenlängen bei z.B. 10 MHz von 200 bis 300 µm. Üblicherweise wird die minimal zu detektierende Fehlergröße mit der Hälfte der Wellenlänge angegeben.
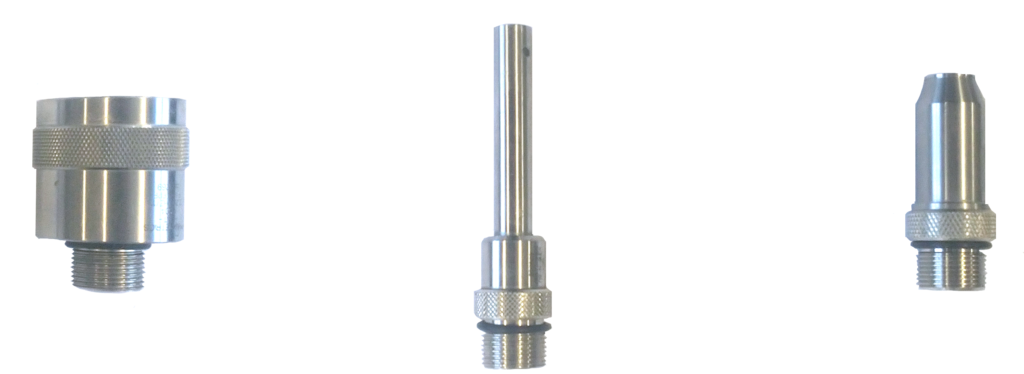
Bei der Prüfung von Materialien mit höheren Schallgeschwindigkeiten (Stahl – 5.900 m/s, Keramik – 10.000 m/s) werden daher Prüfköpfe mit höheren Prüffrequenzen eingesetzt. Die Prüfköpfe haben zumeist eine Bandbreite von 100 %. Dies bedeutet, dass ein 5 MHz-Prüfkopf einen 50 %-Abfall (6 dB-Schwelle) der Schallintensität zwischen 2,5 und 7,5 MHz besitzt. Diese Werte sind vom Hersteller in einem Prüfprotokoll dokumentiert.
Die Auswahl des richtigen Prüfkopfes bei der Ultraschall Tauchtankprüfung
Fokussierte Prüfköpfe, die den Ultraschall über eine Linse wie bei einer Lupe bündeln, bringen den Ultraschall in einem Fokuspunkt in das Prüfteil ein und besitzen daher eine höhere geometrische Auflösung als unfokussierte Prüfköpfe. Ein typischer 5 MHz-Prüfkopf besitzt z.B. eine Fokuslänge von 50,4 cm (2 Zoll) und einen Schwingerdurchmesser von 12,7 mm (0,5 Zoll), so dass sich ein Fokuspunktdurchmesser von ungefähr 1mm ergibt. Prüfköpfe mit höheren Prüffrequenzen haben im Allgemeinen kürzere Fokuslängen und kleinere Schwingerdurchmesser als niederfrequenter Prüfköpfe, da einerseits große Schwinger nicht so schnell (= hochfrequent) schwingen können und andererseits höherfrequenter Ultraschall stärker gedämpft wird als niederfrequenter. Die Prüffrequenz ist daher umgekehrt proportional zur Prüfteildicke.
Ultraschall-Tauchtankprüfung mit hoher Prüfempfindlichkeit
Die Prüfung von Innenfehlern in Getriebewellen und die Reinheitsgradprüfung an Stahlproben im Tauchtank zählen zu unserem Spezialgebiet. Die Ultraschallwellen im Tauchtank werden hierbei motorisch gedreht und mit bis zu zwei Prüfköpfen geprüft. Meist erfolgt eine stirnseitige axiale Einschallung sowie eine Einschallung in diverse Radien. Je nach Geometrie der Welle kann eine Senkrecht- oder eine Winkeleinschallung bei der Prüfung der Radien zur Anwendung
kommen.